UV/EB technology is a game changer for low-carbon, energy-efficient coil coating
Following development work since 2005 and the recent launch of our world-first coil coating paint formulations, we are a clear leader in UV/EB coil coating solutions that help our construction industry customers to make significant environmental savings.
Conventional coil coating requires high-temperature processes that use large amounts of energy. The European Coil Coating Association (ECCA) considers UV/EB curing solutions to be the most significant gamechanger in terms of decarbonising the coil coating industry.
In January 2023, the first coils were produced with our UV/EB paint on a customer industrial line, which represented the first ever UV/EB coil coating commercial paint for the construction industry. Our UV/EB paints provide the same product performance as existing technology – including the ability to meet RUV3 and RUV4 (medium to high resistance to UV) standards.
What are the customer benefits?
UV/EB coil coating solutions provide a range of benefits for our coil coating customers. These include:
- significant energy savings in paint curing.
- half the volume of paint required per m2 surface coverage.
- significant carbon emission savings.
- significant reduction in Volatile Organic Compounds (VOCs).
- shorter coating lines with smaller ovens.
- coating lines can run at higher speeds to offer greater output.
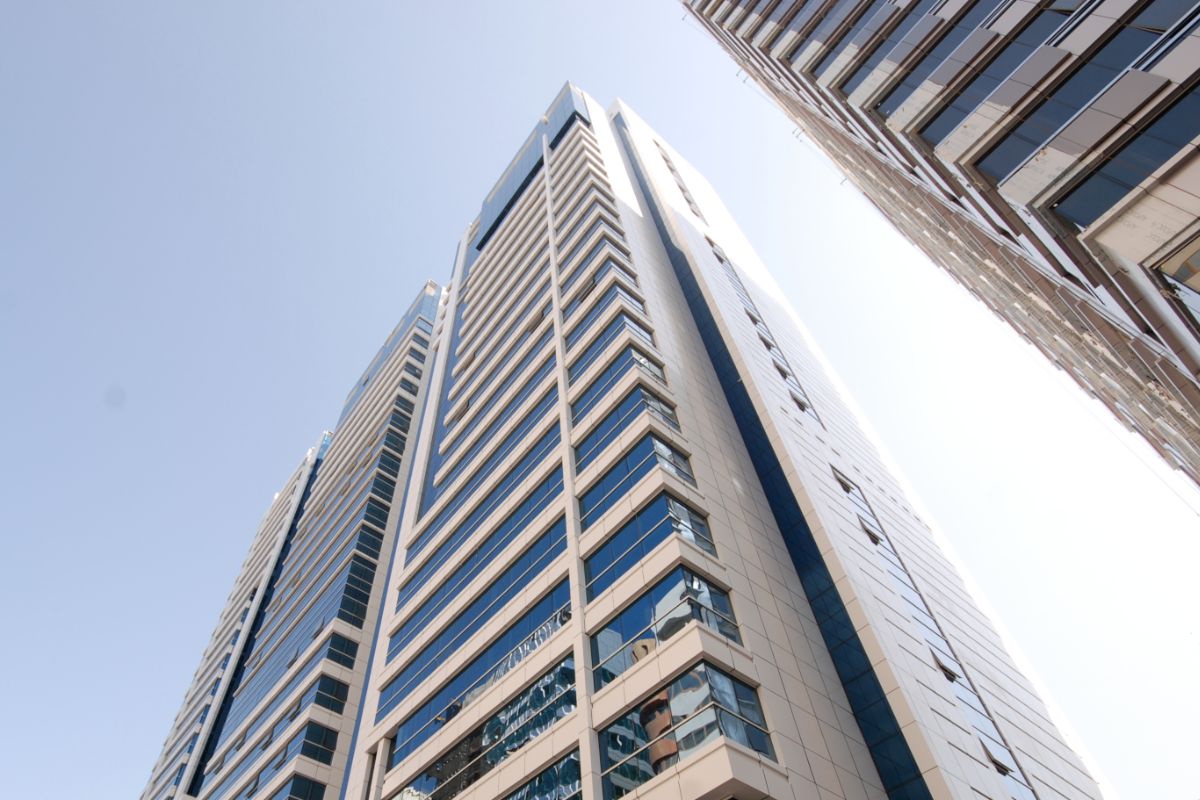
3 Tower offices, photo courtesy of Elval Colour
What are the current UV/EB coil coating applications?
Our first ever UV/EB coil coating commercial paint has been specifically developed for external construction applications, such as façade and roofing products, as well as internal panelling and building accessories. We are currently working closely with customers in Europe on commercial applications.
What are the potential future coil coating applications?
We are working together with a customer in the US to develop UV/EB coating for garage doors and are working with other customers in Europe and in Asia. We are investigating the potential to develop paints that provide RUV5 (super durable resistance to UV) standards. There is also potential to develop coatings for other applications, such as domestic appliances, although this will require the development of paints with different viscosity and mechanical paints than our current UV/EB offering. In addition, the UV/EB cold curing process offers opportunities for us to expand into new coating applications. We have already tested a UV/EB clear varnish coating to provide surfaces with an extra layer of durability.
“The coil coating industry is now aware that UV/EB technology is available, so we are receiving more and more interest from customers around the world,” says Christophe Perin, VP Global Marketing. “At Beckers, we believe in and are investing in UV/EB technology – as demonstrated by the Sustainable Innovation Centre we are developing in Liverpool.”
Contact our press office if you want further information on our UV/EB coatings.